Copyright 2016 James MacNaughton DBA AnnRuel Home Inspections 1skips Way Fairfield, Maine 04937 (207) 861-1227
SERVICE AREA INCLUDES BUT IS NOT LIMITED TO... Albion Augusta Auburn Bangor Belgrade Belgrade Lakes Bowdoin Bowdoinham Bruinswick Burnham Canaan Cape Elizabeth Chelsea China Clinton Cornville Cumberland Detroit Dresden Durham Fairfield Farmingdale Fayette Falmouth Freeport Gardiner Gray Greene Hallowell Hartland Kents Hill Lewiston Lisbon Madison Manchester Monmouth Mount Vernon Newport New Gloucester Norridgewock Oakland Palermo Poland Portland Pittston Pittsfield Readfield Richmond Rome Sidney South Portland Skowhegan Somerville Smithfield St Albans TroyUnity Vassalboro Vienna Waterville Wayne Westbrook Whitefield Windsor Winslow Windham Winthrop
Nachi Certified Home Inspector
ANNRUEL HOME INSPECTIONS LOG HOME INFORMATION
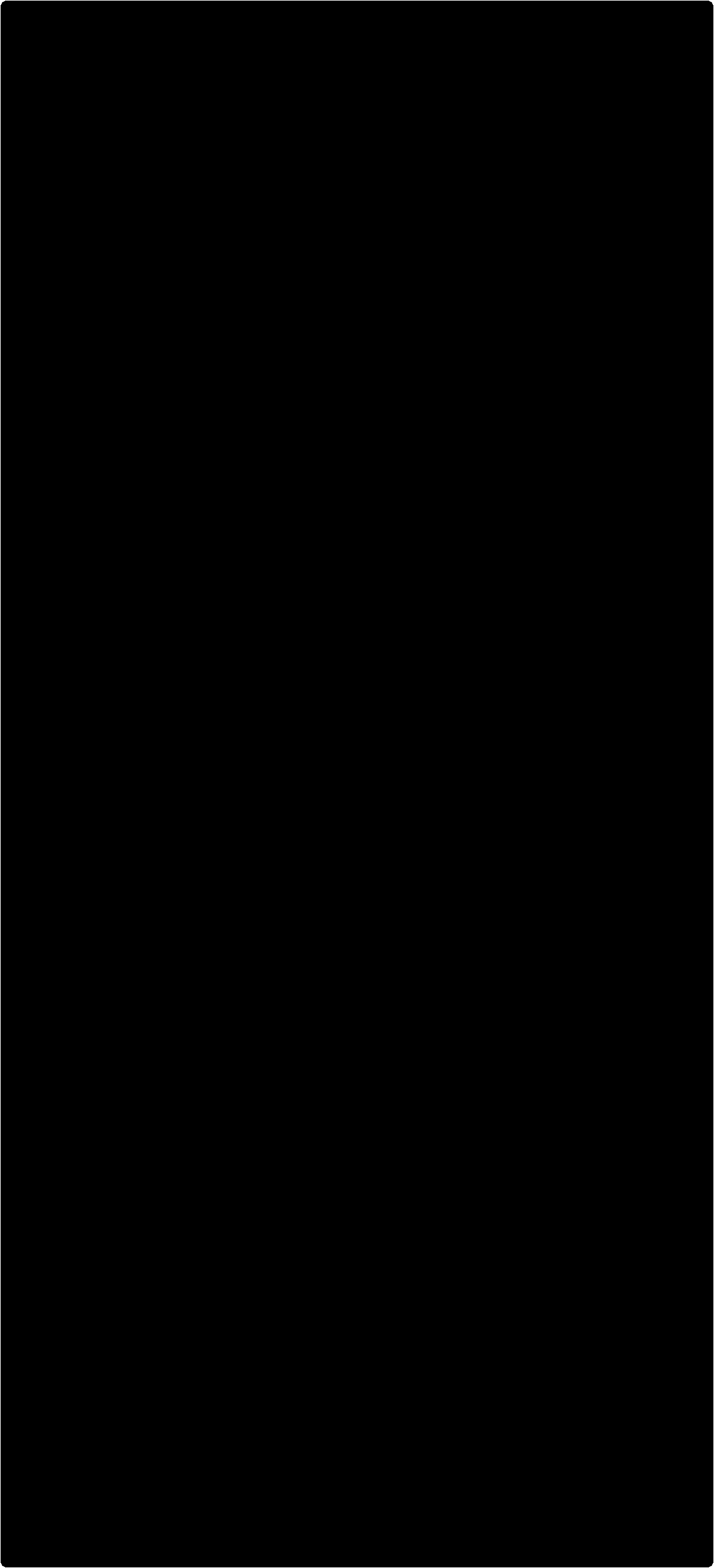
A log Home inspections takes longer than a Stick frame home as the siding needs to be checked closely for proper sealing and if needed resistance drilling needs to be done to check the wood, All chinking needs to be viewed.
LOG HOME DISCLAIMER
Modern caulk-like sealant and its supporting substrate, together commonly known as "chinking," have certain requirements for proper application, including, but not limited, to proper backing and sealant materials and installation, and a minimum sealant thickness, that can be verified only before or during the application process, and which not visible after completion of the chinking application process. The chinking application process was complete at the time of the inspection, and the inspector disclaims these and any other conditions relating to materials and/or installation of the chinking sealant which were not visible at the time of the inspection
Character Cracks
During the time of installation there are often logs used with character cracks and at a later date may appear to be a structural issue. Usually if it was a character crack and sealed prior to or at time of installation and it will be fine but an inspector cannot determine this without having photos provided of the logs at time of installation to determine if it was a character crack or an over- time defect. Before buying a log home make sure to ask to see construction photos taken at time of construction showing any logs in question.
Reasons why Log Home systems fail
The forces that typically cause failure in log homes include
·New Home owners who do not understand the mechanics of a log home
·Rain soil movement, poor landscaping planning or new construction soil movement
·UV and other natural element decay
·Wood-destroying insect activity
·Poor construction practices with regard to design, materials and/or workmanship and log movement. There are too many contractors that will alter a home engineered package so be aware of this practice being done not to the specs the plan called for
·Lack of maintenance and Sealing
·Un-insulated frost heave and settling problems
·Alterations to original engineered plan without consulting original engineer
Perspective Buyer's Instructions to ask Seller
Because of the many variables and liability inherent in a log home, Perspective Buyers may wish to create a list of documents that should be made available to him by the seller for examination. These may include documents showing:
1.the name of the original builder;
2.proof of certified log grading;
3.written settling adjustment records;
4.any special systems installed but not visible at the time of the inspection;
Maintenance records; and additional construction
5.Repair since the original construction.
The Material list is important to have so that the inspector can see the doors and windows used were engineered for this home as well as several other issues.
A great Log Home kit can be of the highest quality while the foundation,electrical and plumbing or after market decks being added can be a major issue
Log cabin maintenance is much more demanding than maintaining a conventional house. But log homes have a couple of issues that need to be addressed differently than a stick-framed house. It’s best to take a slow walk around the exterior of your cabin twice a year and assess the condition of your dwelling. Look carefully and critically at areas where water may be an issue, such as around doors and windows, dormer connections, roof junctions, chimney flashing and the end logs on your log cabin. Check the grounds closely.
A log home should be professionally inspected every year. We usually charge less than half of the original inspection price because we know the house
Cleaning
Look for dark patches where rain has splattered back on the logs and allowed mold or mildew to grow. This is best handled with a simple bleach/water solution mixed in a 50/50 ratio. Scrub the area gently with a soft brush wetted with the solution then hose it off and let dry for a couple of days before re-staining.
Iron Tannate Stains
If you have black stains on your wood that no amount of cleaning by your previous applicators can remove, it is possible that you have iron tannate stains.
Iron tannate stains are the result of a chemical reaction between naturally occurring wood tannates, water, and iron particles. These iron particles most often are introduced to the wood by roof water runoff, incorrect preparation of the wood using steel wool, or simply through the milling process.
This chemical process of iron tannate staining is not only multiplied by chlorine bleach but sometimes initiated by it.
Even more disturbing is that this form of staining is not visible until days or even months after stain is applied, and the appearance of these stains can only be removed or minimized after removal of any finishes, as the problem is on the wood itself. It is recommended that the sealer (lacquer, varnish, polyurethane) be removed prior to using the oxalic acid to remove Iron Tannate stains.
Caulking
Logs will tend to crack and check over time. Over the first year or two as they come into equilibrium with the local humidity and variation over the seasons the logs will swell, contract and check.
This is normal and will not affect the strength or integrity of your logs. For the first several years caulking may be a regular part of your log cabin maintenance routine as the logs settle down to moisture equilibrium.
It’s a good idea to seal up the larger of these checks, anything over about a quarter of an inch to seal out water and bugs. Caulk these with caulk formulated for logs with good stretch and sealant capabilities.
For large checks you should first fill the cavity with backer rod (round foam strips) and then apply the caulk over this. This provides good adhesion for the caulk and the foam allows the normal expansion and contraction of the wood without affecting the caulks bond. Over time this area of log cabin maintenance becomes easier and easier.
Sealing
For large gaps such as around your window and door bucks we have found it best to use expanding foam. If you can feel the cold air coming in around your doors and windows you need to remove the trim boards and check that the bucks have been sealed. These homes need to be re-sealed on a regular basis (on average every 3 to 5 years depending on product used and other factors)
If the existing finish has been properly maintained, it should never require stripping. But if the existing surface has suffered damage (UV degradation, sealant failure, water absorption) applying the most expensive sealant will be a waste of time and money.
Please seek as much information as you can about Log Homes before making the purchase of one.
The Sweep
When we refer to the Sweep of a log we are talking about the bowing. The Bowing is NOT always a hazard and can be structually fine if the moisture levels are low and showing us that the shrinkage has stopped without harming the home
The Taper
The taper is the differance between the logs tip and the butt. again this is not a hazard in the construction stability as long as the logs are alternating properly with the butt on one end and then tip.
Stains
What are the "black specks" appearing on log walls, decks, and asphalt roof shingles? These are actually mature spore masses expelled from fruiting bodies of a fungus known as "shot gun" or "artillery" fungus. Some log homeowners choose to go simply with a clear sealer and no stain (pigment). If you do this, your logs are guaranteed to darken much quicker. For the most part, clear sealers do not offer UV protection. Pigment is what offers UV protection. Although recommended with all waterborne stains, UV-Boost should be automatic if going strictly with a clear. Interior products are different than the exterior clear coat which is applied over the stain. Applying an interior grade acrylic gloss or satin will allow for light reflection and keep the logs much cleaner. When they do get dusty, they can be wiped clean with a damp towel or sponge much easier than with no clear coat. This application will also do a good job at preventing odors (pet, smoke, cooking) from absorbing into the logs. You can apply this product on bare wood or over a stain. No stain known to man will prevent mildew or mold growth, regardless whether they have a mildewcide mixed in or not. Dry wood is what prevents mildew. Certainly, an additional dose of mildewcide which can be added to the stain will make it that much more difficult for mildew to thrive. But it’s no guarantee it won’t ever appear. There are 4 mandated conditions needed to allow for the growth of mildew. They are: the presence of food, moisture, oxygen and temperature. If any of these 4 conditions are eliminated, so will the conditions needed for mildew to grow. The wood is the food source. We have no control over the temperature and we need oxygen. A quality stain and a clear coat finish will help eliminate your logs from absorbing moisture. The magic number for moisture content in your logs is 19%. At 20% or higher, mildew can accumulate. Mildew is not damaging to wood…it’s only unsightly and in most cases, can be cleaned off with relative ease.
Log end Seal
This is a product specifically designed to seal the porous ends of logs and should be applied. some old school contractors will tell you the opposite and they will say this is a good place for the moisture to exit the wood. Run from these contractors
Ants
Shell-Guard (probably the most popular glycol based log preservative in the industry) will kill any carpenter ants, termites or beetles that bite into treated wood. After the Shell-Guard and stain have dried, small critters won’t be effected if there are cracks or open seams that allow them access. Once they bite into the wood, the borate solution disrupts their digestive system, causing them to starve to death.
Use thermal imaging to detect issues before they are visually seen. By the time you see most wood decay over half of the strength has already been lost.
